2.3.1 General Consideration – Personal Protective Clothing/Equipment
Personal protective clothing and equipment should be selected carefully and used in situations where engineering and administrative controls cannot be used or while such controls are being established. These devices are viewed as less protective than other controls because they rely heavily on each employee’s work-practices and training to be effective. The engineering and administrative controls that should always be considered first when reducing or eliminating exposures to hazardous chemicals include:
- Substitution of a less hazardous substance
- Scaling down size of experiment
- Substitution of less hazardous equipment or process (e.g., safety cans for glass bottles)
- Isolation of the operator or the process
- Local and general ventilation (e.g., use of fume hoods)
The Safety data sheet (SDS) will list the personal protective equipment recommended for use with the chemical. The SDS addresses worst-case conditions. Therefore, all the equipment shown may not be necessary for a specific laboratory scale task.
Your supervisor, other sections of this manual or the Director of EHS can assist you in determining which personal protective devices are required for each task. Remember, there is no harm in being overprotected. Appropriate personal protective equipment will be provided to employees.
2.3.2 Protection of Skin and Body
Skin and body protection involves wearing protective clothing over all parts of the body, which could become contaminated with hazardous chemicals. Personal protective equipment (PPE) should be selected on a task basis, and checked to ensure it is in good condition prior to use (e.g. no pinholes in gloves).
2.3.2.1 – Normal Clothing Worn in the Laboratory
Where there is no immediate danger to the skin from contact with a hazardous chemical it is still prudent to select clothing to minimize exposed skin surfaces. Employees should wear long sleeved/long legged clothing and avoid short sleeved shirts, short trousers or skirts. A laboratory coat should be worn over street clothes and be laundered regularly. Laboratory coats are intended to prevent contact with dirt, chemical dusts and minor chemical splashes or spills. If it becomes contaminated it should be removed immediately and affected skin surface washed thoroughly. Shoes should be worn in the laboratory at all times. Sandals and perforated/open-toed shoes are not appropriate. In addition, long hair and loose clothing should be confined.
2.3.2.2 – Protective Clothing
Additional protective clothing may be required for some types of procedures or with specific substances (such as when carcinogens or large quantities of corrosives, oxidizing agents or organic solvents are handled). This clothing may include impermeable aprons and gloves as well as plastic coated coveralls, shoe covers, and arm sleeves. Protective sleeves should always be considered when wearing an apron. These garments can either be washable or disposable in nature. They should never be worn outside the laboratory. The choice of garment depends on the degree of protection required and the areas of the body, which may become contaminated. Rubberized aprons, plastic coated coveralls, shoe covers, and arm sleeves offer much greater resistance to permeation by chemicals than laboratory coats and, therefore, provide additional time to react (remove the garment and wash affected area) if contaminated.
For work where contamination is possible, special attention must be given to sealing all openings in the clothing. Tape can be utilized for this purpose. In these instances caps should be worn to protect hair and scalp from contamination.
Chemical resistant gloves should be worn whenever the potential for contact with corrosive or toxic substances and substances of unknown toxicity exists. Gloves should be selected on the basis of the materials being handled, the particular hazard involved, and their suitability for the operation being conducted. Before each use, gloves should be checked for integrity. Gloves should be washed prior to removal whenever possible to prevent skin contamination. Non- disposable gloves should be replaced periodically, depending on frequency of use and their resistance to the substances handled.
Protective garments are not equally effective for every hazardous chemical. Some chemicals will “break through” the garment in a very short time. Therefore, garment and glove selection is based on the specific chemical utilized. General selection criteria is as follows in the table below.
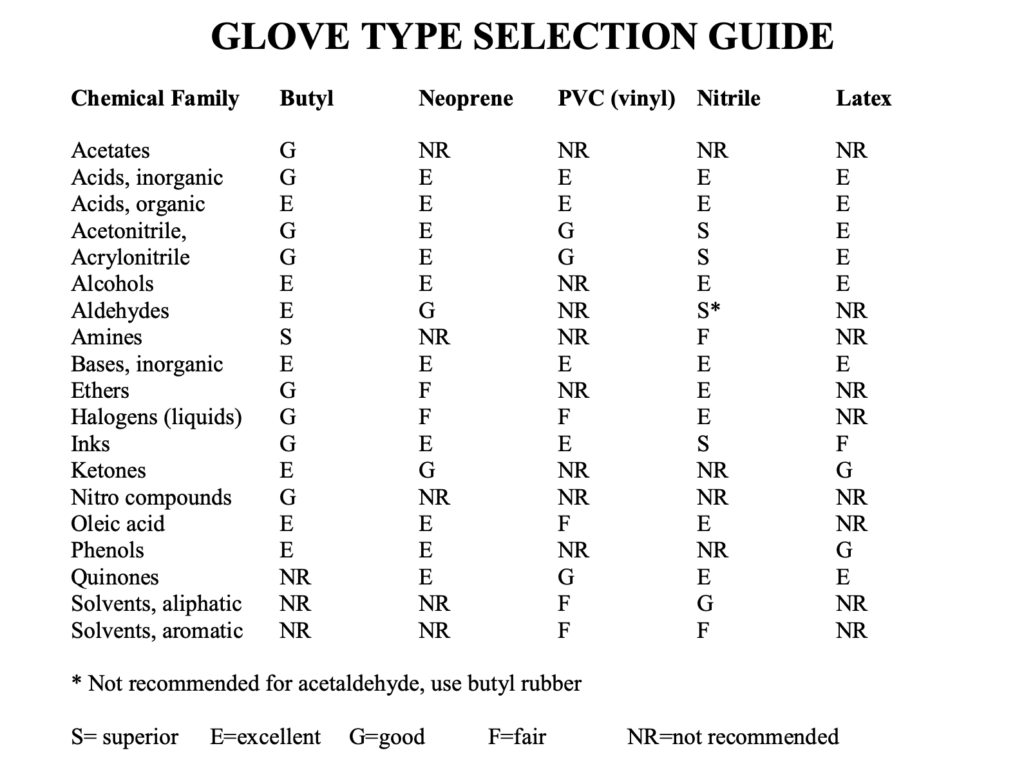
2.3.3 – Protection of the Eyes
Eye protection is required for all personnel and any visitors present in locations where chemicals are handled and a chemical splash hazard exists. Safety glasses, goggles and goggles with face shield should be worn in the laboratory based upon the physical state, the operation or the level of toxicity of the chemical used. Safety goggles effectively protect the eye from solid materials (dusts and flying objects) but are less effective at protecting the eyes from chemical splash to the face. Goggles should be worn in situations where bulk quantities of chemicals are handled and chemical splashes to the face are possible. Goggles form a liquid proof seal around the eyes, protecting them from a splash. When handling highly reactive substances or large quantities of hazardous chemicals, corrosives, poisons, and hot chemicals, goggles with face shield should be worn.
It is recommended, but not required, that contact lenses not be worn in the laboratory. Contact lenses can increase the risk of eye injury if worn in the laboratory, particularly if they are of the gas permeable variety. Gases and vapors can be concentrated under such lenses and cause permanent eye damage. Chemical splashes to the eye can get behind all types of lenses. Once behind a lens the chemical is difficult to remove using an eyewash station.
For more detailed information on eye protection devices, refer to:
ANSI Z87.1 (2015) American National Standard for Occupational and Educational Eye and Face Protection, available from American National Standards Institute, Inc., 1430 Broadway, New York, NY 10018
2.3.4 – Protection of the Respiratory System
Inhalation hazards can be controlled using ventilation or respiratory protection. Check the label and SDS for information on a substance’s inhalation hazard and special ventilation requirements. When a potential inhalation hazard exists a substance’s label or SDS contains warnings such as:
- Use with adequate ventilation.
- Avoid inhalation of vapors.
- Use in a fume hood.
- Provide local ventilation
Take appropriate precautions before using these substances. Controlling inhalation exposures via engineering controls (ventilation) is always the preferred method (See Section 2.3.5.1). As with other personal protective equipment, respiratory protection relies heavily on employee work-practices and training to be effective.
Use of Respirators:
Respirators are designed to protect against specific types of substances in limited concentration ranges. Respirators must be selected based on the specific type of hazard (toxic chemical, oxygen deficiency, etc.), the contaminant’s anticipated airborne concentration, and required protection factors.
Types of respiratory protective equipment include:
- Particle-removing air purifying respirators
- Gas and vapor-removing air purifying respirators
- Atmosphere supplying respirators
Respirators are not to be used except in conjunction with a complete respiratory protection program as required by OSHA. If your work requires the use of a respirator, contact your supervisor or the Director of EHS. See Section 1.9 for additional information as well as OSHA’s employee voluntary use of respirators standard 29CFR1910 subpart I.
2.3.5 Laboratory Safety Equipment
2.3.5.1 – Chemical Fume Hoods
In the laboratory the chemical fume hood is the primary means of controlling inhalation exposures. Hoods are designed to retain vapors and gases released within them, protecting the laboratory employee’s breathing zone from the contaminant. This protection is accomplished by having a curtain of air (approximately 100 linear feet per minute) move constantly through the face (open sash) of the hood. Chemical fume hoods can also be used to isolate apparatus or chemicals that may present physical hazards to employees. The closed sash on a hood serves as an effective barrier to fires, flying objects, chemical splashes or spattering and small implosions and explosions. Hoods can also effectively contain spills, which might occur during dispensing procedures particularly if trays are placed in the bottom of the hoods.
When using a chemical fume hood keep the following principles of safe operation in mind:
- Keep all chemicals and apparatus at least six inches inside the hood (behind sash).
- Hoods are not intended for storage of chemicals. Materials stored in them should be kept to a minimum. Stored chemicals should not block vents or alter airflow patterns.
- Keep the hood sash at a minimum height (4 to 6 inches) when not manipulating chemicals or adjusting apparatus within the hood.
- When working in front of a fume hood, make sure the sash opening is appropriate. This can be achieved by lining up to arrows placed on the sash door and hood frame. This sash opening will ensure an adequate air velocity through the face of the hood.
- Do not allow objects such as paper to enter the exhaust ducts. This can clog ducts and adversely affect their operation.
Follow the chemical manufacturers or supplier’s specific instructions for controlling inhalation exposures with ventilation (chemical fume hood) when using their products. These instructions are located on the products SDS and/or label. However, it should be noted that these ventilation recommendations are often intended for non-laboratory work environments and must be adapted to suit the laboratory environment as well as the specific procedure or process.
If specific guidance is not available from the chemical manufacturer or supplier, or if the guidance is inappropriate for the laboratory environment, contact the Director of EHS and/or review the hood use guidelines in the table below. These guidelines are based on information readily available on a chemical’s SDS:
- Applicable workplace exposure standards [Threshold Limit Values (TLV) or Permissible Exposure Limits (PEL)];
- Acute and chronic toxicity data (LD50 and specific organ toxicity); and
- Potential for generating airborne concentrations (vapor pressure).
These terms are defined in the glossary of terms. The guidelines outlined in the table below should not be considered as necessary or appropriate in every case, but as reasonable “rules of thumb”.
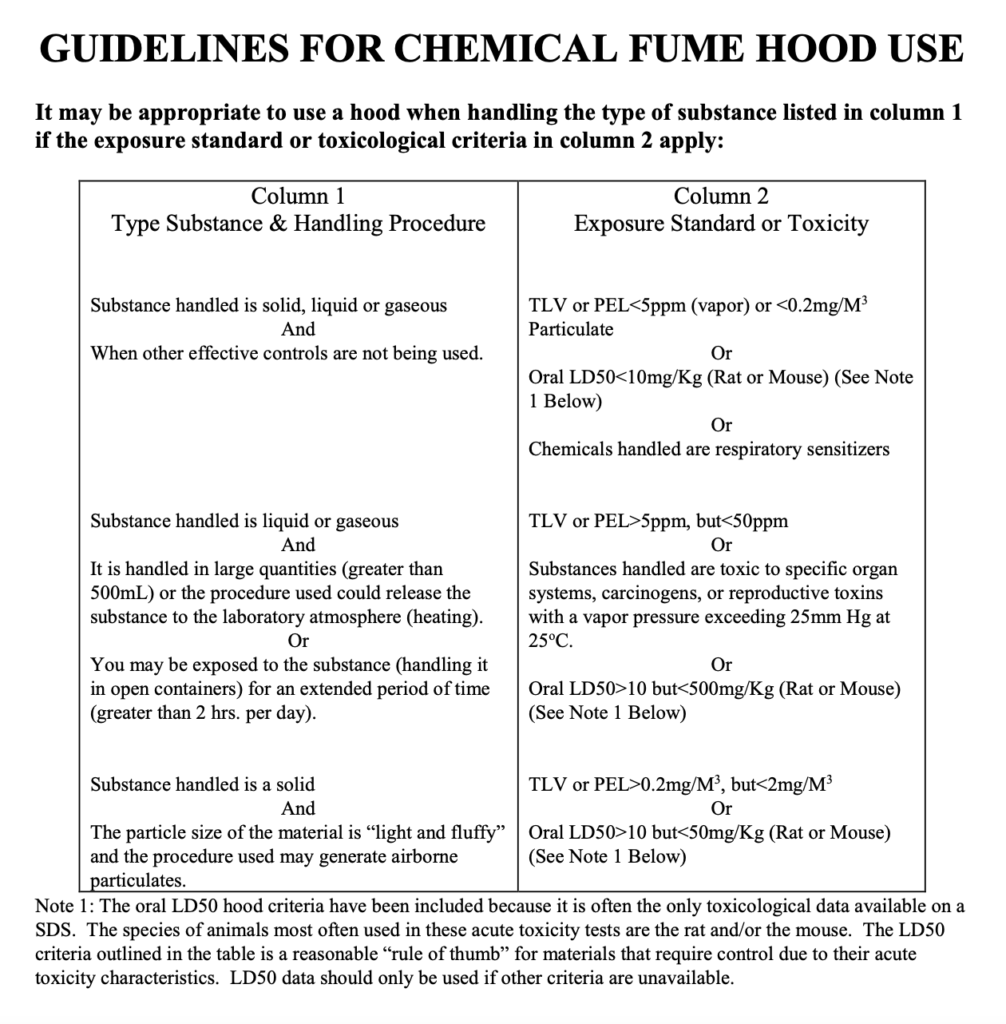
2.3.5.2 – Eyewashes and safety showers
Whenever chemicals have the possibility of damaging the skin or eyes, an emergency supply of water must be available. All laboratories in which bulk quantities of hazardous chemicals are handled and could contact the eyes or skin resulting in injury should have access to eyewash stations and safety showers. As with any safety equipment, these can only be useful if they are accessible, therefore:
- Keep all passageways to the eyewash and shower clear of any obstacle (even a temporarily parked chemical cart).
- Eyewashes should be checked routinely to be certain that water flows through it.
- Showers should be checked routinely to assure that access is not restricted and that the start chain is within reach.
- The flow through the safety showers should be tested periodically to ensure sufficient flow (approximately 60 gallons per minute).
Physical plant employees perform testing of eyewash and safety showers on an annual basis. Test tags are attached and labeled on the date of each inspection.
2.3.5.3 – Fire Safety Equipment
Fire safety equipment easily accessible to the laboratory must include a fire extinguisher (type ABC), fire blankets and/or automatic extinguishing systems. Fire safety and emergency equipment is contained on the emergency carts located on each floor of Hall-Atwater Laboratory. Familiarize yourself with the location and contents of these carts. Inform the Director of EHS if you use any equipment or notice any items missing or in disrepair.