Wesleyan University attempts to minimize employee respiratory exposure to potentially hazardous chemical substances through engineering methods (such as local exhaust ventilation or administrative control). It is recognized, however, that for certain situations or operations, the use of these controls may not be feasible or practical, under these circumstances or while such controls are being instituted, or in emergency situations, the use of personal respiratory protective equipment may be necessary. A sound and effective program is essential to assure that the personnel using such equipment are adequately protected.
An effective respirator program requires the following components:
- Exposure assessment
- Respirator selection
- Medical approval and surveillance
- Fit testing
- User training
- Inspection/repair
- Cleaning/disinfections
- Storage.
Each of these program components is required by OSHA’s respiratory protection standard (29 CFR 1910.134) in all situations where respirators are used. If you are contemplating work which would require the use of a respirator or have questions concerning the use of respirators, contact the Director EHS wnelligan@wesleyan.edu to make arrangements for assessment of the situation.
1.9.1 Respiratory Protection Program
This program element addresses the respiratory protective program required under 29 CFR 1910.134(a)(2):
“A respirator shall be provided to each employee when such equipment is necessary to protect the health of such employee. The employer shall provide the respirators which are applicable and suitable for the purpose intended. The employer shall be responsible for the establishment and maintenance of a respiratory protection program, which shall include the requirements outlined in paragraph (c) of this section. The program shall cover each employee required by this section to use a respirator.”
Purpose: Prevent injury from exposure to airborne contaminants in the laboratory and the Hazardous Waste Container Storage Area (CSA).
Objectives: Provide employees with an appropriate Air Purifying Respirator (APR) with cartridges appropriately selected to control airborne hazard exposures encountered in the laboratory and the CSA. Train employees in respirator use; assure that the respirator continues to fit properly, and that the employee is medically capable of wearing it.
Scope: Covers hazardous chemical spills or uncontrolled chemical releases in the facility only; no normal laboratory activities require respirators. Building engineering equipment provides respiratory protection for normal laboratory activities, i.e., fume hoods, ventilation, etc.
Responsibilities:
- The Safety Officer is responsible for arranging: Selection and purchase of respirators, maintenance of an adequate supply of cartridges, initial and update training, annual fit-testing and annual medical surveillance.
- Each employee is responsible for familiarity with and use of their respirator, cartridge selection for specific hazards required for each work activity they undertake, carrying of spare cartridges to the job site, cartridge replacement when needed, and for cleaning and repairing the respirator when needed.
Procedure/Steps:
- The EHS Department has determined that combination HEPA/organic vapor/acid mist cartridges are appropriate for most emergency response, and maintains a supply of these to fit the respirators used. If a specific job requires another cartridge, the Safety Officer will provide it.
- Annually, the Safety Officer will:
- Arrange for a HAZWOPER update training session, including a respirator fit test.
- Arrange for medical surveillance (physical exam) for assessment of continued capability to use a respirator.
- The Safety Officer will conduct or arrange training of any new employee on the use of a respirator prior to the employee first undertaking emergency response activities requiring one.
- Each employee will bring any issues or concerns about respirators, or conditions which may require respirators, to the attention of the Safety Officer immediately upon noting them.
- Each employee will:
- Check for respirator functionality prior to using it.
- Verify that the cartridge selection matches the hazard(s).
- Use a respirator whenever needed or whenever potential exists.
- Use a respirator at all times when collecting samples of potentially asbestos-containing materials that could release asbestos filters.
- Clean the respirator regularly, and replace cartridges as necessary, at least at theend of each day of use.
- Repair the respirator, or replace missing parts as necessary.
- The Safety Officer will document all respirator training sessions, fit testing, medical surveillance, and retain this information in the employee’s personnel file.
1.9.2 Inspection Checklist for Purifying Respirators
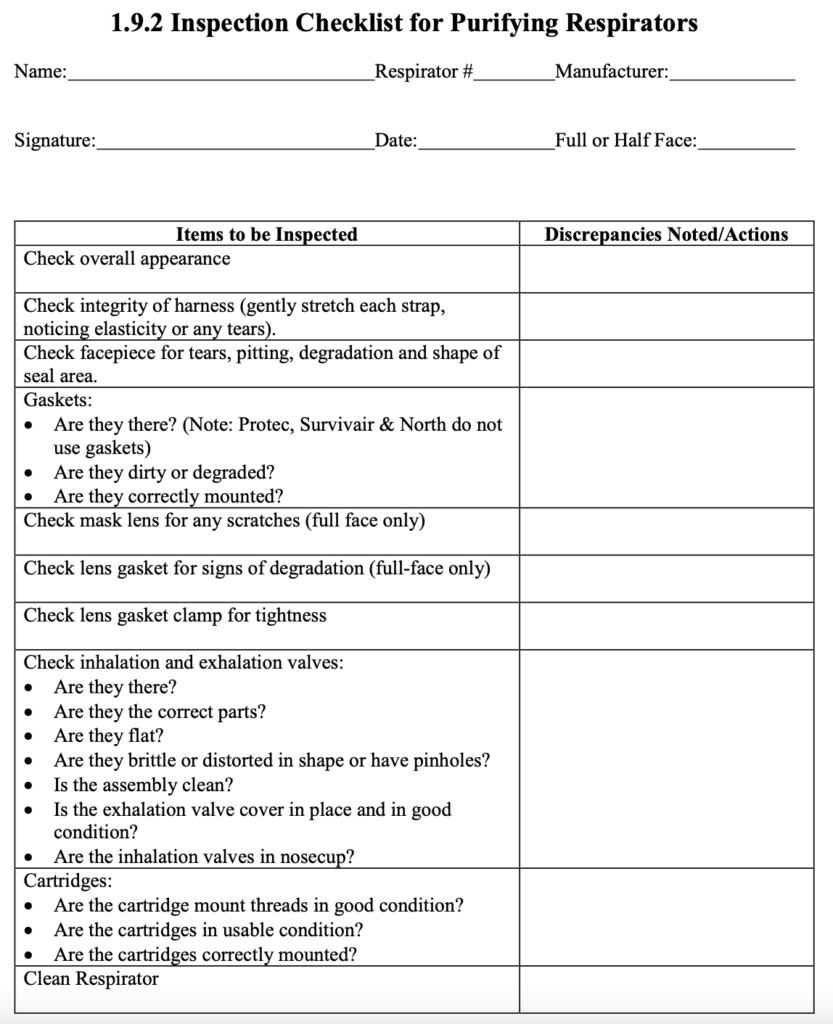