1.5.1 – Chemical Safety Training
All employees exposed to, or potentially exposed to, hazardous chemicals while performing their laboratory duties must receive information and training regarding the standard, the chemical hygiene plan and laboratory safety. Our training consists of annual safety lectures delivered by the Director of EHS or his/her designated substitute. You are required to verify in writing that you have read and understand this document and have attended approved Safety Training Lectures prior to initiating laboratory work. The training and information will be provided when an employee or student is initially assigned to a laboratory where hazardous chemicals are present, and also prior to assignments involving new hazardous chemicals and/or new laboratory work procedures.
The training and information program will describe the following:
- Physical and health hazards of various classes of laboratory chemicals handled;
- Methods/procedures for safely handling and detecting the presence or release of hazardous chemicals present in the laboratory
- Appropriate response in the event of a chemical emergency (spill, overexposure, etc.);
- Chemical safety policies; and
- Applicable details of the Chemical Hygiene Plan (such as the standard operating procedures for using chemicals).
When an employee is to perform a non-routine task presenting hazards for which he or she has not already been trained, the employee’s supervisor will be responsible for discussing with the employee the hazards of the task and any special measures (e.g. personal protective equipment or engineering controls) that should be used to protect the employee. Dry runs of complicated or new procedures should be carried out to perfect techniques.
Every laboratory worker should know the location and proper use of available protective clothing and equipment, and emergency equipment/procedures. Information on protective clothing and equipment is contained in Section 2.3 of this manual.
1.5.2 – Chemical Safety Information
There are numerous sources of chemical safety information. These sources include:
- Online through Wesleyan University Chemical Environmental Management System (CEMS) https://cems.wesleyan.edu/CEMS/SearchSDS
- Special health and safety reference literature available in the Wesleyan University Science Library
- The labels found on containers of hazardous chemicals
- The substance’s Safety Data Sheet (SDS)
- Laboratory signs
In addition, your supervisor is available to provide safety information. Each of these sources is now discussed in greater detail. SDS’ of all chemicals are accessible on the Internet (http://www.ilpi.com/msds/). Hard copies are available in Room 120A – Hall-Atwater Laboratory.
1.5.2.1 – Safety Reference Literature
Wesleyan University’s EHS Staff maintain a library of reference materials addressing chemical health and safety issues. One of the references contains all applicable chemical workplace exposure standards and recommended exposure levels. Another reference contains a copy of OSHA’S laboratory safety standard and its appendices. Safety data sheets (SDS) received from suppliers is available in Hall-Atwater Laboratories room 120A.
1.5.2.2 – Container Labeling
All containers of hazardous chemicals, which could pose a physical, or health hazard to an exposed employee, must have a label attached. As part of OSHA’s recent revision of its Hazard Communication Standard, 29 CFR 1910.1200, chemical manufacturers and imported chemicals are required as of June 1st, 2015 to be labeled consistent with the United Nations’ Globally Harmonized System of Classification and Labelling of Chemicals (GHS). The new standard requires labels that quickly convey hazards visually through pictograms along with instructions for handling the hazardous material.
Labels on purchased hazardous chemicals must include:
- The common name of the chemical or product identifier
- The name, address and emergency phone number of the company responsible for the product
- Signal word
- Hazard Statement(s)
- Precautionary Statement(s)
- Pictogram(s)
There are only two signal words “danger” and “warning” to be used on a hazardous material label, with “danger” used to indicate a greater and “warning” used to indicate a lesser hazard. Only one signal word should be used on a label irrespective of the number of hazards, with “danger” being present if it describes any of the hazards.There are only two signal words “danger” and “warning” to be used on a hazardous material label, with “danger” used to indicate a greater and “warning” used to indicate a lesser hazard. Only one signal word should be used on a label irrespective of the number of hazards, with “danger” being present if it describes any of the hazards.
Hazard statements are specific to the hazard class and describe the nature of a particular hazard. When multiple hazard classifications exist, hazard statements should reflect each of the hazards, when possible, or be consolidated to remove redundancy.
Precautionary statements provide you with additional safety information to help you protect yourself while working with this substance and fall under four categories: prevention; response; storage; and disposal. Prevention precautionary statements includes recommendations for personal protective equipment to be used to minimize exposure when handling the material. Response precautionary statements typically include first aid and cleanup instructions in case of exposure or spillage of the hazardous material. Storage and disposal precautionary statements provide suggested storage and chemical disposal instruction.
If you find a container with no label, report it to your supervisor. You should also report labels that are torn or illegible so that the label can be replaced immediately. Existing labels on new containers of hazardous chemicals should never be removed or defaced, except when empty! If you use secondary working containers that will take more than one work shift to empty, or if there is a chance that someone else will handle the container before you finish it, you must label it. This is part of your responsibility to help protect co-workers.
Read the label each time you use a newly purchased chemical. It is possible the manufacturer may have added new hazard information or reformulated the product since your last purchase, and thus altered the potential hazards you face while working with the product.
All employees involved in unpacking chemicals are responsible for inspecting each incoming container to insure that it is labeled with the information outlined above. The Director of EHS should be notified if containers do not have proper labels.
1.5.2.3 – Safety Data Sheets (SDS)
A Safety Data Sheet, often referred to by its acronym SDS, is a detailed informational document prepared by the manufacturer or importer of a hazardous chemical which describes the physical and chemical properties of the product. Information included in a SDS aids in the selection of safe products, helps employers and employees understand the potential health and physical hazards of a chemical and describes how to respond effectively to exposure situations.
The format of a SDS may vary but there is specific information that must be included in each sheet. It is useful to review this information to increase your ability to use a SDS:
All Safety data sheets should include the following information:
Section 1, Identification of the manufacturer and the product should include:
- Manufacturer’s name, address and telephone number
- Number to call in case of emergency involving product
- Chemical name or product identifier or other means of identification
- Trade name and synonyms
- Chemical family and formula
- Recommendations and restrictions on usage
- CAS# (Chemical Abstract Service) for pure materials
Section 2, Hazards identification describes the various hazard classifications of the product, label elements, signal word, and precautionary statements.
Section 3, Composition/information on ingredients provides information on ingredients and trade secret claims and should include:
- Common name and synonyms
- Chemical name and formula
- CAS# (Chemical Abstract Service) for pure materials
- Impurities and stabilizing additives which are both classified and contribute to theclassification of the substance
- Concentrations or concentration ranges for ingredients that contribute to theclassification of the substance
- Trade secret statements
- Manufacturers may withhold certain information as proprietary (such as hazardousingredients) on a SDS if the information is considered a trade secret. The Director of EHS has a legal right to obtain this information from the manufacturer to evaluate the potential health risk if potential overexposure or adverse health effects are suspected.
Section 4, First-aid measures describes effects of exposure, both acute and delayed, and necessary measures to take for each route of exposure. Any special treatments or indication of other necessary medical attention is provided.
Section 5, Fire-fighting measures describes appropriate fire-fighting equipment and relevant hazards such as:
- Extinguishing agent – water, dry chemical, foam, halon, etc.
- Unusual fire and explosion hazards, toxic fumes and combustion products
Section 6, Accidental release measures gives instructions for the steps to be taken in case of an accidental release or spill and waste disposal methods. The steps normally include information on containment, evacuation procedures and waste disposal as appropriate. The statements on the SDS are very general; more specific information is available from your supervisor or the Director of EHS.
Section 7, describes handling and storage procedures to be taken with the material. Information may include statements, such as: keep container closed; store in a cool, dry, well-ventilated area; keep refrigerated (caution: flammable solvents require a “flammable storage refrigerator”); avoid exposure to sunlight; chemical incompatibilities, etc.
Section 8, Exposure controls/personal protection describes the protective equipment for the individual who might have to work with the substance and exposure limits (OSHA permissible exposure limit (PEL), Threshold Limit Value (TLV), etc., and any other recommended exposure limit provided by the manufacturer.) This section normally describes worst-case conditions; therefore, the extent to which personal protective equipment is required is task dependent. Contact your supervisor or the Director of EHS for specific instructions, if you are unsure.
- Respiratory equipment: dust mask; chemical cartridge respirator; self-contained breathing apparatus
- Ventilation: local; general; special
- Protective gloves: type; fabrication material
- Eye protection: goggles; face shield
- Other protective equipment
Section 9, describes the physical and chemical properties of the material.
- Boiling point
- Vapor pressure
- Vapor density
- Flash point
- Specific gravity
- Percent volatile
- Evaporation rate
- Decomposition temperature
- Solubilities
- Appearance and Odor
- pH
- Auto-ignition temperature
- Lower and upper explosive limits (UEL/LEL)
Section 10, Stability and reactivity describes reactivity data; that is, the material’s ability to react and release energy or heat under certain conditions or when it comes in contact with certain substances.
- Stability: stable; unstable; conditions to avoid
- Incompatibility: materials to avoid
- Hazardous decomposition products
- Hazardous polymerizations and reactions: conditions to avoid
Section 11, Toxicological information describes the known health hazards associated with the material, likely routes of exposure, applicable exposure limits and symptoms/health effects associated with overexposure. This information will help the user and medical personnel recognize if an overexposure has occurred.
- Threshold Limit Value
- Effects of overexposure: headache, nausea, narcosis, irritation, weakness, etc.
- Primary routes of exposure: inhalation, skin, and ingestion
- Cancer or other special health hazards
- Emergency and first aid procedures for ingestion, inhalation and skin or eye contact – UN number
- UN proper shipping name
- Transport hazard class(es)
- Packing group, if applicable
- Environmental hazards
- Bulk and special precautions which a user needs to be aware of or comply with
Section 12, Ecological information (non-mandatory) describes ecotoxicity, bioaccumulation and degradation potential, mobility in soil, and other adverse effects.
Section 13, Disposal considerations (non-mandatory) describes waste residues and methods of disposal for both the material and its container.
Section 14, Transport information (non-mandatory) gives information relevant to the transportation of the material such as:
- UN number
- UN proper shipping name
- Transport hazard class(es)
- Packing group, if applicable
- Environmental hazards
- Bulk and special precautions which a user needs to be aware of or comply with
Section 15, Regulatory information (non-mandatory) gives safety, health and environmental regulations specific for the product.
Section 16, Other information includes revision or preparation date for SDS
1.5.2.4 – Laboratory Signs
Prominent signs of the following types should be posted in each laboratory:
- Telephone numbers of emergency personnel/facilities, supervisors, and laboratory workers;
- Door signs that list emergency contacts, principal investigator and senior lab personnel;
- Signs identifying locations for safety showers, eyewash stations, other safety and first aid equipment, and exits;
- Warnings at areas or equipment where special or unusual hazards exist.
1.5.2.5 – Hazard Communication Standard Pictograms
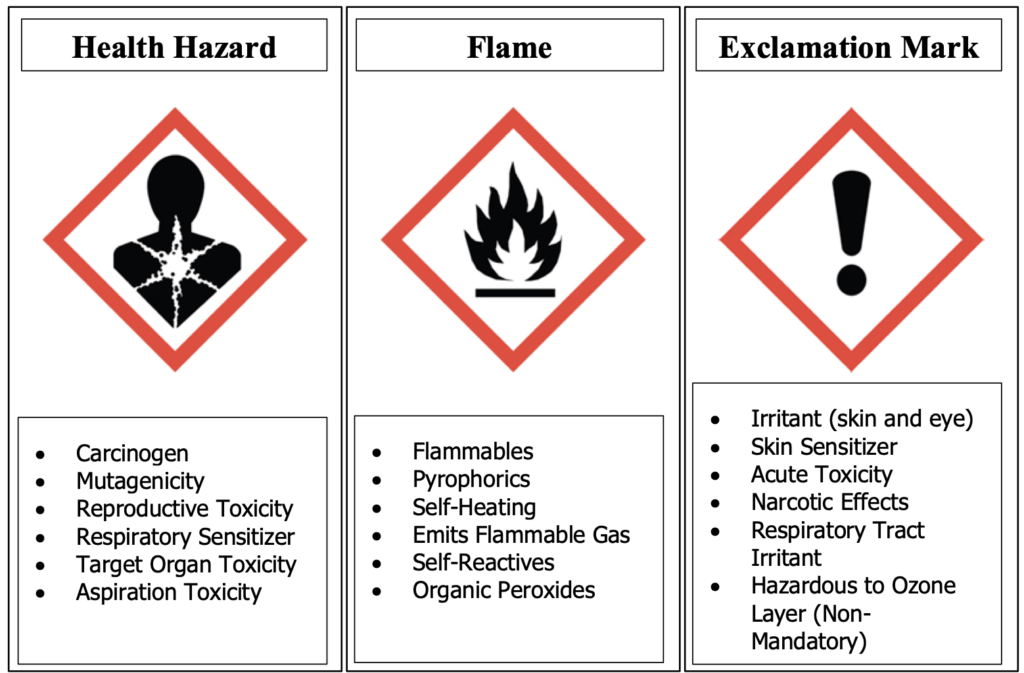
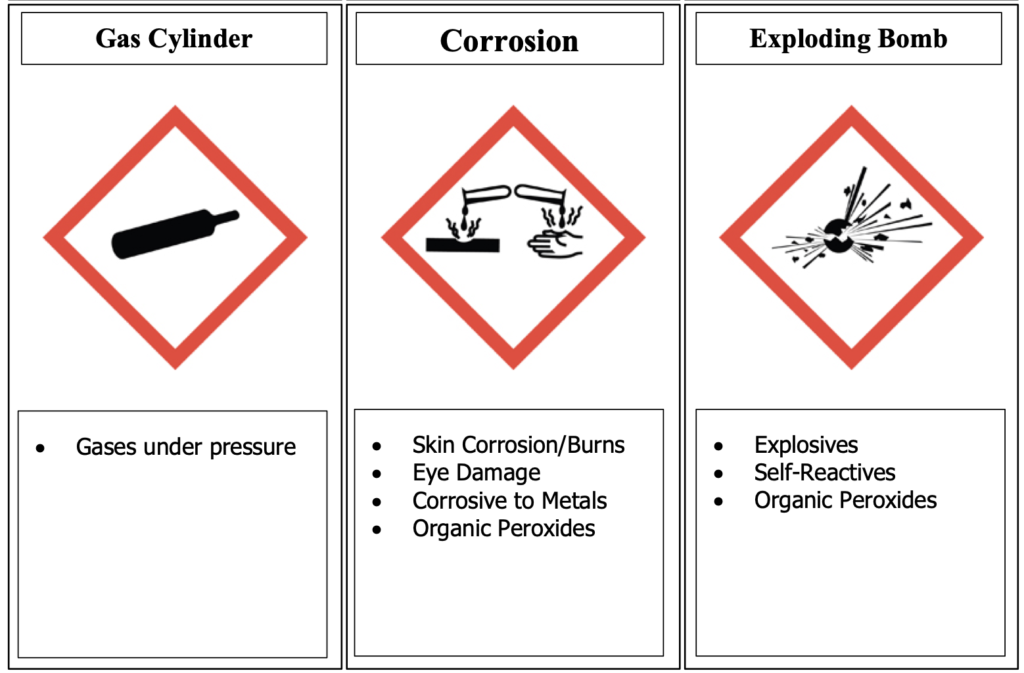
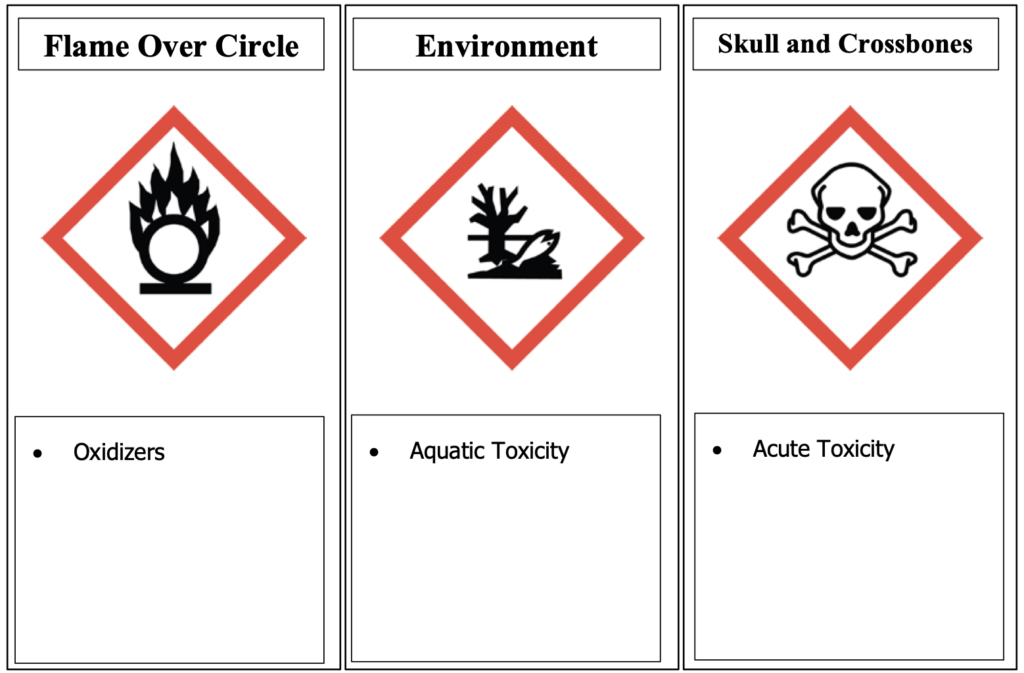